![manufacturing[1]](https://clouderp.org/wp-content/uploads/2022/10/manufacturing1.jpg)
Noch nie gab es ein so umfangreiches Angebot an Technologien, die in der Lage sind, Fertigungssysteme erheblich zu verbessern. Leider ist oft unklar, welche Systeme von diesen Technologien profitieren können, und nur selten gibt es einen klaren Weg, wie man die Vorteile ihrer Anwendung nutzen kann. Was soll ein Unternehmen also tun?
Die Trends in der Fertigungstechnologie haben sich in den letzten Jahren auf verschiedene Projekte konzentriert, die die Produktivität im Back-Office, die verbesserte Planung und die Automatisierung auf Werksebene betreffen. Die Verbesserung einzelner Prozesse ist schön und gut, aber die Verbindungspunkte zwischen Betriebs- und Geschäftsplanungssystemen sind trotz der unzähligen Artikel, die über die Konvergenz von Betriebstechnologie (OT) und Informationstechnologie (IT) geschrieben wurden, nach wie vor einer der am meisten unterschätzten Investitionsbereiche. Allzu oft bedeutet “Konvergenz” eine Tabellenkalkulation am Verbindungspunkt, die eine Lücke füllt, aber weit davon entfernt ist, eine echte organisatorische Zusammenarbeit zu ermöglichen.
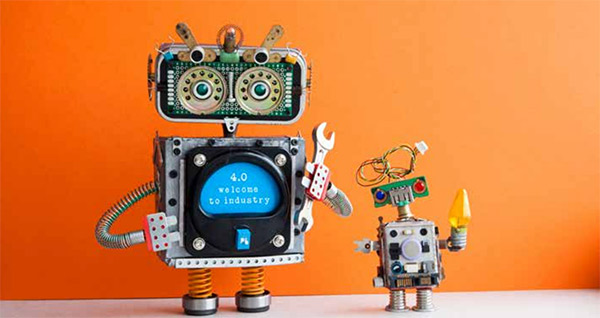
Digitale Transformation – eine Ziffer nach der anderen
In den letzten Jahren ist der Begriff “Industrie 4.0” in den Werkshallen, in der Lieferkette, im Lager, in der IT-Abteilung und in den Büros von Führungskräften der Fertigungsindustrie lautstark zu hören. Er hat sogar die Ohren von Händlern und Kunden erreicht. Der Lärm von Industrie 4.0 hat sich etwas gelegt, aber er wurde durch ein ähnliches Maß an Aufregung um den Begriff “Digitale Transformation” ersetzt.
Nicht alle Strategien und Bemühungen zur digitalen Transformation sind gleich. Digitalisierung und Digitalisierung werden oft fälschlicherweise für austauschbar gehalten, aber es handelt sich um völlig unterschiedliche Konzepte. Digitalisierung ist definiert als die Automatisierung eines Prozesses mit Hilfe eines Computers oder einer anderen verwandten Technologie. Die Digitalisierung bezieht sich auf die Umstellung einer Reihe von manuellen Tätigkeiten auf einen weniger arbeitsintensiven, effizienteren und wiederholbaren Ansatz. Alternativ dazu umfasst die Digitalisierung das Überdenken von Prozessen und Strategien in einer Weise, die sie effektiver und anpassungsfähiger macht. Die Digitalisierung ist die Veränderung, die sowohl unmittelbare Ergebnisse liefert als auch den tatsächlichen Wandel im Unternehmen vorantreibt.
Die Digitalisierung sollte nicht entmutigt werden, da sie einen soliden ROI liefern kann. Ganze Technologien haben sich entwickelt, um Wege zur Verbesserung des Status quo zu finden. Die robotergestützte Prozessautomatisierung (Robotic Process Automation, RPA) ist im Kern ein leistungsfähiges Werkzeug, das zur Entlastung von Mitarbeitern eingesetzt werden kann, deren Arbeit einen hohen Anteil an sich wiederholenden manuellen Tätigkeiten umfasst. Wer würde nicht gerne den endlosen Papierkram bei der Bearbeitung von Rechnungen abschaffen, der das Öffnen mehrerer Systeme und das Hin- und Herschreiben von Daten erfordert? RPA kann effektiv eingesetzt werden, um die Ausführung bestimmter Prozesse zu verbessern, ohne diese Prozesse grundlegend zu verändern. Fairerweise muss gesagt werden, dass RPA irgendwann KI und andere Techniken einsetzen kann, die es gut in ein Digitalisierungsprojekt einbinden können, aber die meisten aktuellen RPA-Bestrebungen dienen ausschließlich der Digitalisierung.
Die Umstellung von Prozessen, die für die Digitalisierung erforderlich sind, ist von Natur aus ein schwierigeres Unterfangen. Es scheint nie Zeit für eine Neugestaltung zu sein. Es gibt immer restriktive Einwände gegen die Veränderung. Der Übergang von bestehenden zu neuen Prozessen birgt in der Regel ein Risiko in Form einer möglichen Unterbrechung der Geschäftsabwicklung. Angesichts knapper Investitionsbudgets, unterbesetzter IT-Abteilungen und der Abkühlung der Produktionswirtschaft müssen sich die Hersteller fragen, ob es jetzt an der Zeit ist, die Herausforderungen der Digitalisierung anzunehmen.
Wie bei so vielen Fragen lautet die Antwort “es kommt darauf an”. Einige Hersteller, die über sehr isolierte Geschäftsmodelle verfügen und denen keine Störung droht, können wahrscheinlich mit einem schrittweisen Digitalisierungsansatz auskommen. Der Ansatz “nur ein bisschen besser” wird vielleicht nicht ewig funktionieren, aber vielleicht eine Zeit lang. Hersteller, die versuchen, in Sektoren mit hohem Störungsgrad zu überleben und zu gedeihen, sollten einen tiefgreifenderen Digitalisierungsansatz in Betracht ziehen.
Chancen, die an den Schnittstellen der Systeme verborgen sind
Die Mehrheit der Hersteller scheint irgendwo dazwischen zu liegen. Die meisten haben zumindest ein allgemeines Verständnis für die Vorteile, die eine echte digitale Transformation bringen kann. Über 90 % aller Unternehmen geben an, dass sie in irgendeiner Form eine digitale Transformation anstreben. Auch wenn das Streben nach geschäftlicher und digitaler Transformation bei jedem Hersteller anders ist, gibt es zweifellos einige gemeinsame Themen, Best Practices, Erfolgsgeschichten und Misserfolge sowie Lektionen, die es zu lernen gilt.
In der Regel mangelt es nicht an unterstützenden Systemen, die nicht mehr zukunftsfähig sind und mit heroischen Anstrengungen und gekreuzten Fingern zusammengehalten werden. Diese Systeme werden irgendwann einzeln an die Spitze der Listen rücken und ihre Mängel werden behoben werden. Doch wie kann ein Fertigungsunternehmen die unzähligen zusätzlichen Möglichkeiten der digitalen Transformation für Systeme priorisieren, die nicht so offensichtlich veraltet sind?
Die Reibungspunkte zwischen den Systemen können attraktive Möglichkeiten für eine echte Digitalisierung bieten. Eine unzureichende Zusammenarbeit zwischen den Disziplinen Planung und Betrieb schränkt die Fähigkeit eines Fertigungsunternehmens ein, die Anforderungen der Kunden zu erfüllen. Hersteller haben oft keinen zeitnahen und genauen Einblick in den Betriebsstatus der geplanten Produktion. Dieser Mangel an Einblicken beeinträchtigt die Fähigkeit der Produktion, effektiv auf unvorhersehbare Kundensituationen, Bestandsengpässe, Anlagenausfälle und Unterbrechungen der Lieferkette zu reagieren.
Trotz des großen Interesses an der OT/IT-Konvergenz haben nur wenige Unternehmen viel getan, um die Zusammenarbeit zwischen Systemen auf Geschäftsebene und Systemen auf Betriebsebene zu optimieren. Die Koordinierung mit der Ausführungsseite der Fertigung wird wohl der wichtigste kurzfristige Gewinner der Investitionen in die digitale Transformation sein. Das Füllen dieser Lücken mit Tabellenkalkulationen mag sich wie ein Fortschritt anfühlen, kann aber tatsächlich einen echten Fortschritt verhindern. Tabellenkalkulationslücken sind Systemanpassungen, die unter dem Radar fliegen und die tatsächliche Koordination zwischen Planung und Betrieb nicht fördern.
Es gibt gute Nachrichten an der Front der digitalen Transformation, die potenziell allen Arten von Herstellern helfen können, unabhängig davon, wo sie in Bezug auf die Transformation stehen. Da die zugrunde liegenden Technologien und Lösungen für die digitale Transformation noch nicht ausgereift sind, gibt es viele erfolgreiche Projekte und Geschäftsanwendungen, die einen schnellen ROI bieten und keine großen Investitionen erfordern. Wenn Sie damit beginnen, Informationen oder Daten aus beiden Komponenten der Wertschöpfungskette zusammenzuführen und dem Betrieb zur Verfügung zu stellen, erhält Ihr Betriebsteam umsetzbare Erkenntnisse, die zu besseren Entscheidungen, höherer Effizienz, niedrigeren Kosten, zufriedeneren Kunden und höheren Gewinnspannen führen.
Einige Beispiele für Digitalisierungsprojekte, die eingeleitet werden können, um echte Ergebnisse zu erzielen:
- Integrale Erweiterung von Enterprise Resource Planning (ERP) in den Betrieb – Produktionsausführungssysteme, die auf weit verbreiteten bedienerzentrierten Shopfloor-Schnittstellen und integriertem IoT basieren, können Einblicke im Produktionstempo liefern. Diese Lösung ersetzt eine Vielzahl manueller Datenerfassungssysteme und komplexer, übermäßig starrer Schnittstellen zu Manufacturing Execution System (MES) oder anderen Fertigungslösungen.
- Enterprise Quality Management System (QMS) – Allzu oft bestehen die Systeme zur Unterstützung der Qualitätsbemühungen in der Fertigung aus zahlreichen anderen, unzusammenhängenden Systemen, die sich im Laufe der Zeit entwickelt haben. Ein stärker integrierter Ansatz für die Qualitätsplanung und den Qualitätsbetrieb kann den manuellen Aufwand im gesamten Unternehmen verringern, was zu einer echten Ursachenanalyse führt und letztlich die tatsächlichen Qualitätskosten senkt.
- Koordinierte Materialverwaltung vom Lager bis zur Fertigung und wieder zurück – Automatisierte Lösungen, die eine koordinierte Lieferung von benötigtem Komponentenmaterial, die Identifizierung des verbrauchten Materials und die Kennzeichnung von Fertigwaren für die endgültige Auslieferung ermöglichen, sind für das anpassungsfähige Fertigungsunternehmen unabdingbar geworden. Die operative Verbesserung der Materialverwaltung ist die grundlegende Möglichkeit, aber diese Fähigkeit ist entscheidend für den wachsenden Bedarf an Rückverfolgbarkeit und Produktgenealogie.
Viele frühe Bemühungen, die man als Digitalisierung bezeichnen könnte, drehen sich um die Automatisierung einiger bestehender Funktionen oder Prozesse. Es könnte sich dabei um die Auswertung von Datenmengen handeln, die mit früheren Ansätzen nicht ausgewertet werden konnten. Diese Digitalisierungsbemühungen können tatsächlich die notwendige Grundlage für die nachfolgende Beschleunigung der Digitalisierungsaktivitäten sein. Es ist wichtig, mit der größeren Vision der wirklichen Revolution voranzuschreiten, die sich aus der Anwendung derselben Energie und Techniken auf Lösungen ergeben wird, die zuvor nie in Betracht gezogen wurden. Echte Prozessveränderungen und disruptive Geschäftsmodelländerungen werden letztendlich der Lohn sein. Unabhängig davon, ob es sich um Digitalisierungs- oder Digitalisierungsbemühungen handelt, gibt es reale Möglichkeiten für Fortschritte an planerischen und betrieblichen Anschlusspunkten. Hersteller, die Maßnahmen ohne größere Unterbrechungen ergreifen, können Vorteile in Form von Renditen in mehrfacher Höhe erzielen.
Leave a Reply